Find your ideal job:
Not sure which job?Just click search:
KPI. A Specialist Recruiter of Engineering & Manufacturing People
When you choose KPI Engineering and Manufacturing, you're partnering with a dedicated team committed to delivering excellence and ensuring the perfect match for your engineering & operational talent needs. Let's build the future of engineering together.
Our Vision:
To become the premier provider of engineering and operational talent solutions, bridging the gap between innovative companies and exceptional talent.
Our Mission:
To deliver customised recruitment services that connect engineering and operational professionals with organisations requiring their specialised skills, fostering mutual growth and success.
Services we offer:
- Permanent Placement: Finding the right fit for full-time engineering positions across various industries.
- Contract Staffing: Providing skilled engineers for temporary assignments.
- Executive Retained Search: Sourcing top-tier engineering executives for leadership roles.
- Project-Based Hiring: Assembling engineering teams for specific projects or time-bound requirements.
- Consulting Services: Offering expert advice on hiring strategies, market trends, and talent management.
Testimonials.
Advertise your vacancy HERE.
Sign Up For Job Alerts
Why choose KPI Engineering & Manufacturing?
Industry Expertise:
Our team has extensive experience in the engineering sector, ensuring we understand the specific needs and challenges of engineering roles.
Comprehensive Screening:
We conduct thorough assessments, including technical skill evaluations, to ensure candidates meet the highest standards.
Extensive Network:
Our vast network of engineering, operational professionals and industry contacts helps us find the perfect match quickly and efficiently.
Customised Solutions:
We tailor our recruitment process to meet the specific needs of each client, ensuring the best fit for both the employer and the candidate.
Commitment to Diversity:
We actively promote diversity and inclusion in engineering, helping clients build innovative and diverse teams.
Latest job listings. View all
Maintenance Engineer
Join a growing, forward-thinking food manufacturing business in Wrexham Area as a Mechanical & Electrical Maintenance Engineer! This is a fantastic opportunity for an experienced engineer to step into a key role focused on keeping production running smoothly and safely while driving continuous improvement.
The Role
As a Maintenance Engineer, you'll be responsible for both preventative maintenance and emergency breakdowns on a variety of factory machinery and equipment. You'll play a hands-on role in machine installations, overhauls, repairs, and upgrades-ensuring all plant machinery is safe, compliant, and running at optimum performance.
Key Responsibilities
Carry out preventative maintenance and emergency repairs
Diagnose faults and implement cost-effective solutions
Support with installation and commissioning of new equipment
Ensure compliance with Health & Safety and Food Safety standards
Collaborate with Technical, Operations, Engineering, and HR teams
Actively promote and implement continuous improvement initiatives
Work with contractors and suppliers when needed
Maintain detailed and accurate maintenance records
What We're Looking For
NVQ Level 3 minimum in Engineering (HNC/18th Edition with Part P preferred)
Solid experience in a similar Maintenance Engineering role
Strong understanding of food processing equipment and wrapping machines
Confident fault-finding and problem-solving ability
Good interpersonal and communication skills
A proactive, hands-on attitude with a passion for continuous improvement
Able to work well under pressure in a fast-paced manufacturing environment
Why Apply?
Be part of a collaborative and values-driven team
Varied and challenging role with opportunities to grow your skills
Work in a business that values health, safety, and food quality
Long-term career opportunity with a growing company
CNC Miller
CNC Miller Programmer
We are working with a organisation who have been established for over 35 years and have gone from strength to strength. My client specialise in servicing a wide spectrum in all moulding materials. They are toolmakers and precision engineers specialising in the design and manufacture of all production tooling. We are currently looking for experienced CNC Miller Programmer to join this company based in Lancashire.
Key skills required of the CNC Miller Programmer:
- Must have over 4+ years hands on working experience as a CNC Miller
- Must have 4+ years experience with Setting and Operating Mills
- Experience as a Programmer is required around 5+ year
- Ability to write programs from scratch
- Any experience of Fanuc or Heidenhain is required
- Ideally Apprentice trained
The successful CNC Miller Programmer's main duties would include, programming and setting CNC Machining centres producing low volume, high value complex components to tight tolerances by studying engineering drawings and Computer generated Models and applying knowledge of materials and machining. This is an excellent company they 'do' what they say and there is no doubt the rate will be reviewed and increased for the right person.
Hours 37 per week: Monday - Thursday 7.30am - 4.30pm and Friday 7.30am - 3:00pm
Job Types: Full-time, Permanent
Pay: £17.00-£18.00 per hour
Expected hours: 37 per week
Benefits:
- Company pension
- On-site parking
Schedule:
- 8 hour shift
- Day shift
- Monday to Friday
- Overtime
Experience:
- CNC Miler: 4 years (preferred)
- CNC programming: 4 years (preferred)
- Fanuc or Heidenhain: 4 years (preferred)
- Setter and Operator: 4 years (preferred)
Work Location: In person
Technical Operator
Technical Operator
Runcorn – £35,000
Mon – Fri 15.00 – 23.00
- We are seeking a passionate Technical Operator is to Operate, Maintain, Improve and Repair our new state of the art clean room within our Runcorn facility. You will support the delivery of operational KPI’s (Productivity, Quality, Safety, Health and Environment, Cost, Delivery). Working within an autonomous team the Technical Operator will drive excellent standards of production delivery and continuous improvement, whilst always protecting a safe and sustainable environment.
You will be required to champion specific skills and coach others. You will have a basic understanding of key cost drivers in the clean room and will grow this in line with your project management skills - As the Technical Operator you will be at the heart of our clean room ensuring that all KPI’s are managed
- Working closely with Sales, Supply Chain, Ecommerce and the production teams to ensure we deliver excellence to our customer
- Technical - Knowledge and application of technical skills to Operate, Maintain, Improve and Repair (OMIR) equipment. This allows production targets to be met safely, at the right level of quality and on time
- Understand the principles of mechanism and motion and be able to conduct changeovers on our bottling and pouch lines
- Identify and troubleshoot problems with the packing machines. Perform basic repairs, such as fixing jams, and resolving minor mechanical issues.
- Safety - Utilise appropriate safety and environmental procedures for people, processes, materials, products and equipment to ensure a safe working environment for the whole team
- Environment - Reduce costs due to waste and minimise impact to health, safety and the environment through working to eliminate waste
- Quality - Ensure that all aspects of Quality within the area of responsibility are in accordance with our Quality procedures to protect and promote the brand and product
- Leadership - Promote the development of a highly effective and autonomous team through strong communication, leading by example and conflict management, whilst keeping focused on goals and targets
- Coaching – Champion specific skills within the team and coach them to others in order to drive excellence
- Continuous Improvement - Use performance measures to identify and prioritise losses in production area. Apply rigorous Cost Deployment and the Zero loss concept to eliminate losses
- Problem Solving - Has the ability to identify, prioritise and address problems using appropriate tools and techniques that eliminate recurrence.
- Production Output - Agree production plan targets and review performance in order to drive functional goals at individual and team level.
- Business Awareness - Understanding of the need to meet changing demands and the role of marketing and product innovation in growing the business and increasing the company's share.
Skills & Experience Required
- Core Engineering Skills – Background in Maintenance, Bench fitting and/or Machining
- Experience of working as part of an extended team within the manufacturing sector
- Strong leadership and communication skills
Experience of manufacturing in a Fast-Moving Consumer Goods Company
Experience as a team member within a project Management team with an awareness of project management tools and techniques - Growth Mindset eager to embrace challenges and continuously improve processes to help drive our team's success”
Benefits
- Competitive Salary: Rewarding your skills and dedication
- Medical Insurance (CashPlan): Keeping you and your family healthy
- 50% Discount on HTC Products: Enjoy our products at half the price
- On-Site Free to Use Gym: Convenience at your workplace
- On-Site Complimentary Secure Parking: Safe and convenient parking at your workplace.
- 33 Days Annual Leave Inclusive of Bank Holidays
- Shared Success Bonus: Benefit from the company's success
- Company Pension: Secure your future with our pension plan
- Death in Service Benefit (2x Annual Salary)
#INDENG
Electrical PLC Project Engineer
Are you a skilled Electrical Project Engineer with a passion for control systems, PLC/HMI software, and end-to-end project delivery? We're working with a leading engineering solutions provider who are on the lookout for a driven Electrical Project Engineer to join their growing team.
The Role
As an Electrical Project Engineer, you'll play a pivotal role in designing control system hardware, developing PLC/HMI software, and delivering technical documentation to support a range of exciting and bespoke engineering projects. Reporting to the Electrical Engineering Manager, you'll work across departments, liaise with clients, and provide both onsite and overseas support during commissioning phases.
Key Responsibilities
-
Attend project kick-off meetings to gather key requirements.
-
Interpret technical specifications to meet both customer expectations and internal standards.
-
Carry out control system hardware design using SEE/EPLAN electrical design software.
-
Generate PLC and HMI software and conduct functional testing.
-
Create and maintain accurate documentation packs for all equipment.
-
Provide technical input for sales quotations on non-standard projects.
-
Support After Sales with service visits and commissioning both in the UK and abroad.
-
Ensure compliance with Machinery Directives, COSHH, ATEX, and Health & Safety policies.
What We're Looking For
-
Strong communication skills - written and verbal.
-
Proactive, self-starter who thrives both independently and within a team.
-
Excellent time management and organisational abilities.
-
Customer-focused with a practical, solutions-driven mindset.
-
Prior experience in electrical project engineering with PLC/HMI development.
-
Working knowledge of EPLAN or SEE Electrical (or similar).
-
Flexibility to travel for commissioning and service visits when required.
About the Company
A market leader in the design, manufacture, and supply of material handling solutions. Known for their innovation and commitment to quality, they work with clients across a broad range of industries, delivering tailored engineering solutions that truly make a difference.
Maintenance Technician (Nights)
Maintenance Engineer - Electrical/Mechanical | £42,000 | Telford | Permanent Nights
Are you an experienced Maintenance Engineer looking for your next challenge? We're recruiting on behalf of a leading manufacturing business in Telford, seeking a skilled Electrical/Mechanical Maintenance Engineer to join their team on permanent nights (20:00 - 06:00, Mon-Fri).
What You'll Be Doing:
-
Conducting electrical and mechanical maintenance on overhead gantry cranes and associated systems
-
Ensuring safe, efficient plant and equipment operations to minimise downtime
-
Diagnosing faults, interpreting electrical diagrams, and executing effective repairs
-
Maintaining detailed maintenance records and organising planned maintenance around production schedules
-
Servicing hoists and lifting equipment, ensuring compliance with legal and safety standards
-
Purchasing essential spares and working with suppliers to improve equipment design and reduce costs
-
Working autonomously and demonstrating initiative in a fast-paced environment
What We're Looking For:
-
City & Guilds Level 2/3 in a relevant discipline
-
17th or 18th Edition Electrical Installations qualification
-
Strong electrical and mechanical fault-finding skills
-
Comfortable working at heights and with lifting equipment
-
Proactive, safety-conscious, and highly organised with good communication skills
Salary & Hours:
-
£42,000 per annum
-
Permanent Nights: 20:00 - 06:00, Monday to Friday (30 min unpaid break)
Project Engineer
Project Engineer
Mon – Thurs 08.00 – 16.30 Fri 08.00 – 12.30
Newcastle-under-Lyme
Up to £40K DOE
The engineering department is responsible for all technical aspects of design, development, production & test. This includes, but is not limited to, documentation, processes, records and registers, tooling & equipment, electronic systems & tools etc.
- The department creates, develops, completes & maintains
- RFQ documentation to support the quotation process (BoMs, Labour Estimates, Feasibility Checks, Tooling Evaluation)
- ROM documentation to support early customer engagement activity
- Production process documentation to facilitate accurate, correct and repeatable production methods
- Visual and physical build aids and jigs to facilitate accurate, correct and repeatable production methods
- 2D drawings and documentation of products and assemblies
- 3D models and documentation of products and assemblies
- Physical test jigs and fixtures to facilitate testing of products and assemblies
- Software testing programs to facilitate testing of products and assemblies
- Engineering is required to support other departments where applicable either onsite or offsite
- The Project Engineer is required to tackle and manage engineering projects that can range from simple product designs to very complex assembly projects with cross departmental deliverables
- Collate this information to form reports, documents, designs of new products and assemblies, relevant outputs and deliverables internally and externally
- Also required to produce sometimes complex prototype products, assemblies, jigs and fixtures to support projects and other activities directly and indirectly
- Supporting the engineering department as needed across a multi-disciplined team is a key component of the role and frequently the project engineer may be required to perform quotations, production process creation/evaluation/review, fault finding & correction etc.
- Liaise internally and externally with departments, customers, suppliers to facilitate effective communication and ensure deadlines are met (remote via video conference and local in person)
- Travel to other H+S locations or customer/supplier locations globally as required to attend project and design meetings
- Provide support to the quotation process by creating BoMs and labour estimations, feasibility reports, and tooling reviews
- Provide support to the RoM process, estimating components, pricing, labour and processes to provide the required information
- Design and develop new products and assemblies to meet the requirements of the project, and manage all documents and processes associated with the project
- Create 2D design drawings and documents using CAD
- Create 3D design models and documents using CAD
- Produce prototype products and assemblies, liaising with relevant internal and external departments to meet performance requirements and deadlines
- Support the engineering dept as needed in any required activity to flex with the demands of the business
Essential Skills/Experience
- Due to the nature of projects, candidates must be able to pass a British 5 year minimum security check (dual passports will be not be considered)
- Minimum of 3-5 years’ experience in and engineering role within a relevant industry
- Good knowledge and working experience of cable assembly, wire harnessing, electro-mechanical assembly is a must
- Computer literate with good fundamental knowledge of the Microsoft Office 365 workspace
- CAD knowledge and experience 2D/3D (Solid Edge/Solid Works/AutoCAD/Harnware/Catia)
- Excellent communication skills and ability to form relationships with multicultural colleagues (must have excellent written and spoken English skills)
- Excellent organisational skills and the ability to manage own time and priorities
#INDENG
Mechanical Tool Design Engineer
Mechanical Tool Design Engineer
Leicester
Monday – Friday (flexi time)
£28,000 - £42,000 DOE
33 Days Holiday (including Bank Holidays)
Our client is a leading special purpose engineering cutting tool manufacturer specialising in the design and manufacture of cutting tools for the Aerospace and Automotive sectors.
Due to continued success, we have a permanent job Vacancy for a Mechanical Design Engineer, working in a Precision Engineering environment.
This will be a varied and interesting job role but with a focus on the design of broach cutting tools.
- Producing design Layouts for quotation purposes
- Produce the technical design and specification of the broach tool to meet customer’s enquiry
- Produce 2D and 3D CAD production drawings using Autodesk Inventor
- Help support the Technical Department with root cause analysis of technical issues and provide general design support
- Support the production department with technical queries
Skills & Experience
- The successful applicant should ideally have experience in a previous Engineering Design role using 2D and 3D CAD software ideally Autodesk Inventor
- Minimum qualification is HNC or equivalent in Mechanical Engineering
- Ideally have experience in a Precision Engineering environment
#INDENG
Multi-Skilled Maintenance Engineer
Maintenance Engineer
4 on 4 off (permanent days £48,000) OR
4 on 4 off (permanent nights £54,000)
About The Role
Our sites are ever-demanding, complex and in some cases operate 24 hours a day - so it's vital we have a strong Engineering team who ensure our machines work to the best of their ability. So we can continue to provide great products to our customers, whilst still ensuring speediness. As a Multi Skilled Maintenance Engineer, you will play a vital role in ensuring the smooth operation of our Manufacturing site. You will be responsible for the maintenance, repair, and improvement of our machinery and equipment, ensuring minimal downtime and maximum efficiency. This is a hands-on role that requires strong technical skills and the ability to troubleshoot and solve problems quickly.
Reporting to the Site Engineering Manager your responsibilities will include:
- Conduct routine inspections and preventive maintenance on production equipment, identifying and resolving any potential issues before they cause disruptions
- Respond promptly to machinery breakdowns, diagnose the problem, and perform repairs or coordinate with external specialists when necessary
- Carry out machine adjustments and changeovers to support production line efficiency and minimise downtime
- Monitor and calibrate equipment to ensure accuracy, quality, and safety standards are met
- Collaborate with production teams to identify opportunities for process improvement and provide technical expertise to enhance productivity
- Keep accurate records of maintenance activities, including maintenance schedules, repairs, and spare parts inventory
- Adhere to health and safety guidelines and ensure compliance with company policies and procedures
- Stay updated with industry advancements and new technologies relevant to the role
Skills & Experience
- Qualifications to NVQ level 3 (or equivalent, ONC mechanical/electrical engineering, BTEC level 3 in mechanical & electrical/electronic engineering)
- Strong knowledge of mechanical and electrical systems used in FMCG industry
- Proficient in troubleshooting and repairing industrial machinery, including conveyors, motors, pumps, and packaging equipment
- Proactive approach to maintenance and a commitment to ensuring the highest levels of equipment reliability
- A good understanding of HACCP principles and ideally IEE qualification up to 17th edition wiring regulations would be advantageous
- Excellent communication skills
- Assertiveness with the ability to make decisions on the spot
- A can do attitude and a strong work ethic
Benefits
- Six weeks holiday (including bank holidays)
- 15% discount in our stores available from the day you join us
- Additional 10% discount card for a friend or family member
- Career progression and development opportunities
- Subsidised staff canteen
- Free parking
- Market leading pension and life assurance
- Healthcare/Well-being benefits including Aviva Digital GP
- MyPerks with discounts at high street shops, cinemas and gyms, and lots more
- Long Service Awards
- Optional Payroll charity donations
- Enhanced Family/maternity/parental leave
Mechanical Design Engineer
Mechanical Design Engineer
Location: Ashton-in-Makerfield, Wigan
Salary: Up to £40,000 per annum (DOE)
Job Type: Permanent, Full-time (36.5 hours/week)
Industry: Engineering/Manufacturing
Exciting Opportunity for a Mechanical Design Engineer!
We are seeking an experienced Mechanical Design Engineer to join a well-established and highly respected engineering company in Wigan. This is an excellent opportunity to be part of a dynamic team specialising in the design and manufacture of bespoke packaging solutions, automotive logistics, and lineside material handling equipment for high-profile OEM manufacturers within the automotive and construction industries.
Key Responsibilities:
- Design bespoke vehicle component packaging solutions based on customer-supplied 3D models and design specifications.
- Ensure all designs are fit for purpose, cost-effective, and optimised for manufacturing.
- Prepare 3D models and PowerPoint concept proposals for review.
- Create and release 2D manufacturing drawings and Bills of Materials (BOMs).
- Maintain engagement with customers throughout the design process via electronic communication, Teams meetings, and occasional site visits.
- Successfully manage design projects from inception to final production delivery.
- Support the sales team in securing new business.
- Contribute to the continuous development of the design function.
Requirements:
- HNC/HND/Degree in Mechanical Engineering or equivalent.
- Minimum 3 years' post-graduate experience in a design engineering role within a manufacturing environment.
- Proficiency in SolidWorks with experience in designing mechanical components, steel fabrications, sheet metal, CNC laser-cut parts, and pressings.
- Experience in polyurethane cast mould tooling (preferred but not essential).
- Knowledge of Epicor ERP systems (advantageous but not essential).
- Experience with 3D printing (preferred but not essential).
- Strong communication skills, both verbal and written.
- Existing right to work in the UK is required.
What's on Offer?
- Competitive salary (negotiable based on experience).
- 32 days holiday per year.
- Private health benefits (after qualifying period).
- Company pension scheme.
- Half-day Fridays
#ENGIND
HSE Manager
Health, Safety & Environment Manager
Overview
We are seeking a Health, Safety & Environment (HSE) Manager to ensure the implementation of HSE processes and procedures in our chemical manufacturing, storage, and distribution business. The role involves working closely with various teams to maintain safety, environmental, and quality standards, while also driving continuous improvement as a top Tier COMAH site.
Responsibilities
- Champion and review COMAH regulations to maintain Upper Tier status
- Coordinate Integrated Management Systems with ISO 14001 and ISO 45001
- Manage environmental aspects in accordance with COMAH, EPR, and ISO 14001
- Review, update, and issue new SOPs and procedures
- Facilitate site health & safety and operational committee meetings
- Lead incident, accident, and near miss investigations
- Implement, monitor, and maintain the company's EPR authorizations
- Manage waste disposal/recycling activities on site
- Represent the company at relevant seminars and industry events
- Carry out additional duties as required by the company
Qualifications
- NEBOSH Certificate/Diploma in Health & Safety
- Ideally degree qualified in Process Safety, Chemistry, or Chemical Engineering
- 5-10 years' experience with COMAH at Upper Tier Site & Environmental Permitting Regulations
- Strong leadership and communication skills
- Working knowledge of quality management systems and internal auditing
- Proficiency in Microsoft Office, Teams, Word, Excel, and Outlook
Day-to-day
- Coordinate HSE activities across the site
- Liaise with various internal and external stakeholders
- Conduct audits and checks on HSE management systems
- Provide in-house training related to H&S and environmental aspects
- Participate in incident, accident, and near miss investigations
- Manage waste disposal and recycling activities on site
Benefits
- Competitive salary
- Health and wellness benefits
- Opportunities for professional development
- Dynamic and challenging work environment
If you are a self-driven leader with a passion for maintaining high HSE standards, we encourage you to apply for this exciting opportunity.
Our partners




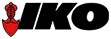

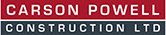
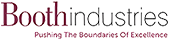
